Mold section
Test pressing in Thailand
Without dispatches from overseas, how can we carry out a check mold inside Thailand…」
There is no domestic manufacturer who carrys out overhaul in Thailand. All parts were ought to be dispatched from other countries where it was produced. Therefore, it takes too much time and cost.
「 By introduction of test mold press into the NFT Thailand factory, we are now able to support you domestically. 」
There is no domestic manufacturer who carrys out overhaul in Thailand. All parts were ought to be dispatched from other countries where it was produced. Therefore, it takes too much time and cost.
Flexible delivery and quality service for prototype mold products
[We immediately need reflector product samples]
To answer the requests from end-user, we are supposed to fabricate prototype mold dies and produce samples as soon as possible. Furthermore, we need to secure quality.
「 Prompt delivery service, original surface treatment. 」
Upon your order, we could provide meeting for layout within a day. Maximum speed designing and producing process allow us to accomplish just in time delivery. In addition, with our original knowhow for surface finishing treatment, we could provide even quality to satisfy our client.
Improvement for lens package void
[We are struggle with getting rid of void]
We are struggle with getting rid of void from lens package transparent compound. It can not be solved even we changed molding conditions over and over again.
[Solved by vacuum unit]
Introduction of manual press AcrossM which has vacuum unit, allows you to digitalize of transfer timing control, pressing process and deaeration. It also contributes easy access to the best condition. Furthermore, considering molding conditions such as the strip quantity per press, dummy cavity, corner R and release angle, NFT mold design made a progress not only for solving void problem but also mold release.
Maximizing the quantity of strip per press devotes to secure profits
[We need to secure profits for general discrete products]
We want to increase maximum quantity of strip to secure profits.
[With changes in mold die design, we could maximize production]
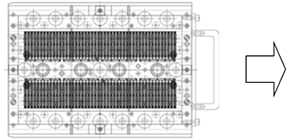
1,344 PKG x 2 LFs = 2,688 PKG / Shot
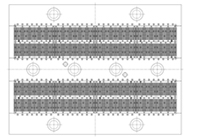
3,536 PKG x 2 LFs = 7,072 PKG / Shot
The thickness of BGA product is easily changed
「We want to change thickness of product simply.」
For conventional BGA products, there is a necessary to change full cavity set to change its thickness. Still we want to change it simply with reasonable cost.
[By changing spacer, we can change thickness easily.]
As a new design, we changed upper cavity specification with inserting structure. Based on EDM precision for cavity top surface and grinding precision for spacer thickness that NFT have, we could answer the request that containing severe standard for thickness.
Lengthen lifespan for retractable pin + sleeve
[lifespan for retractable pin + sleeve is too short.]
Lifespan for retractable pin + sleeve of power package is too short. We cannot avoid opportunity lost, and it makes life cycle cost high.
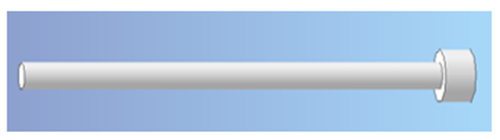
[By hardening retractable pin, making its lifespan tripled.]
Based on our original technology, NFT made retractable pin 2 times harder, and 3 times stay longer
Countermeasure for Abrasion of power package mold
「 Abrasion in gate・runner parts of power package mold die are so harsh, that the lifespan is too short. 」
As a conventional surface treatment, HCR can only afford to achieves HV800~1000, because compound seal for power semiconductor contains plenty of silicon.
[Changing surface treatment method, making its lifespan tripled.]
By changing surface treatment method for gate・runner part, we made it 2 times harder (HV1800~HV2000)and 3 times last longer.
Reducing adjustment time for upper and lower chase dislocation.
[With the conventional way, there is a necessary to do adjustment process for upper and lo wer chase dislocation and it hinders improving productivity.]
The standard for upper and lower chase dislocation is too severe to make fine tuning for us. Even we had done reassembly process, it could not be solved.
[With the conventional way, there is a necessary to do adjustment process for upper and lo wer chase dislocation and it hinders improving productivity.]
We fabricated one-sided guide block which can carry out adjustment on press. Without any changes on other main parts, we are able to solve chase dislocation at reasonable cost and accomplished significant reduction about adjustment time.
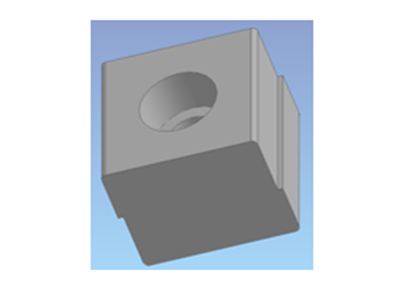
The improvements for flash on leads part
[defective plating caused by the flash on leads part]
We changed frame because of the defectives in plating. Still, it is not solved at all. Is there any improvement from the mold parts side?
[Improvement by polishing on parting surface]
Usual way of polishing parting surface is only for longer direction. As a countermeasure against flash caused by L/F rolling roll part, we adopted shorter direction polishing on parting surface. In conclusion, we made a progress on reducing seepage problem.
Countermeasure for leakage Adding narrow groove
[the leakage for slit package can not be stopped.]
The resin leakage from WBGA slit package products continued and, even it reaches to the ball pad part, we have struggle with it.
[We make it stopped by adding several narrow grooves next to the package.]
Based on NFT’s design and grinding technics, we succeed to adding 2 narrow grooves within 0.5 mm perimeter, to stop leakage of resin.